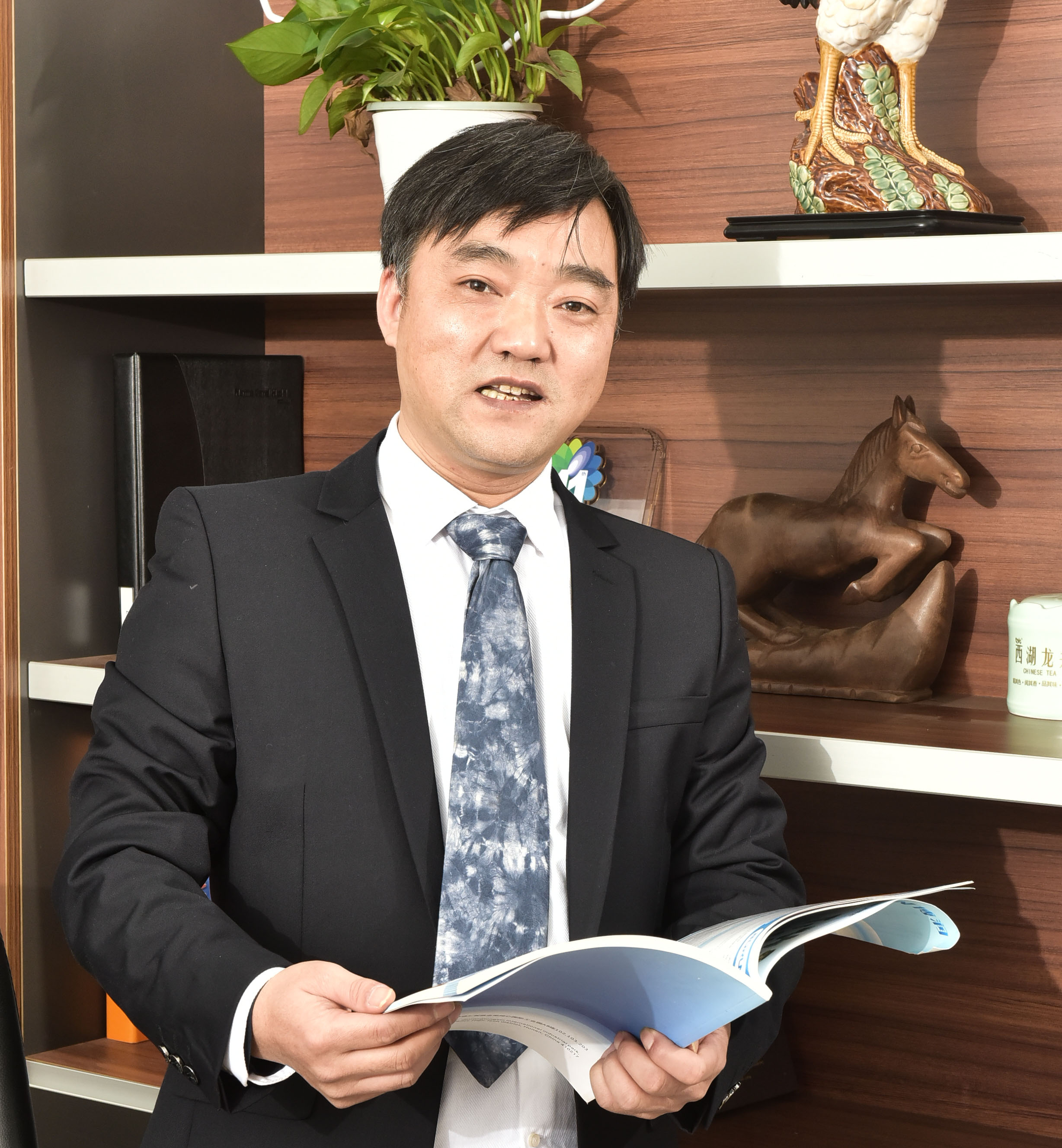
Mr. Tony
Leave a messageMr. Tony
Leave a messagePlastic mold design is based on the correct design of plastic products, and mold design and manufacturing are closely related to plastic processing.The success or failure of plastic processing depends greatly on the mold design effect and the mold manufacturing quality. Then, what structural factors should be considered in the design of plastic mold?
1. Parting surface
The contact surface of the die and the punch when the die is closed.Its position and form are selected, affected by product shape and appearance, wall thickness, molding method, post-processing technology, mold type and structure, demodulation method and molding machine structure, etc.
2. Structural parts
That is, the slide block of the complex mould, the inclined top, the straight top block and so on.Structure design is critical, is related to the life of the mold, the processing cycle, cost, quality, etc., so the design of complex mold core structure on the designer's comprehensive ability the demand is higher, as far as possible the pursuit of more simple, more durable and more economical design.
3. Mold precision
Namely avoid card, precise position, guide pillar, position pin and so on.Positioning system is related to the appearance quality of the products, mold quality and life expectancy, according to the mould structure is different, choose different way of positioning, rely mainly on machining precision control, internal model is mainly targeted at the designer to consider fully, to design more reasonable and easy to adjust positioning way.
4. Pouring system.
The feed passage between the Nozzle of the injection molding machine and the cavity, including the main channel, the shunt channel, the gate and the cooling hole.Especially the selected gate location should be conducive to the molten plastic flows in a good condition with cavity, attached to the products of solid cold runner and sprue feeding when open mold is easy to be out and be removed from the mould (except hot runner mold).
5. The plastic shrinkage rate and various factors that affect the precision of product size.
Such as mold manufacturing and assembly error, mold wear and so on.In addition, when designing the die and injection mold, the process of forming machine and the matching of structural parameters should be considered.
NITONI, As a China Precision Mold Parts, Core Pin, Ejector Pin, Mold punch, Mold parts, Mold Components, Non-standard Precision Parts, Plastic mold parts , press die mold parts, manufactur and supplier,At present, The mould accessories products are mainly divided into Non-standard mold parts, Plastic mould parts, Press die mold parts, Die Springs, welcome to understand the customization.