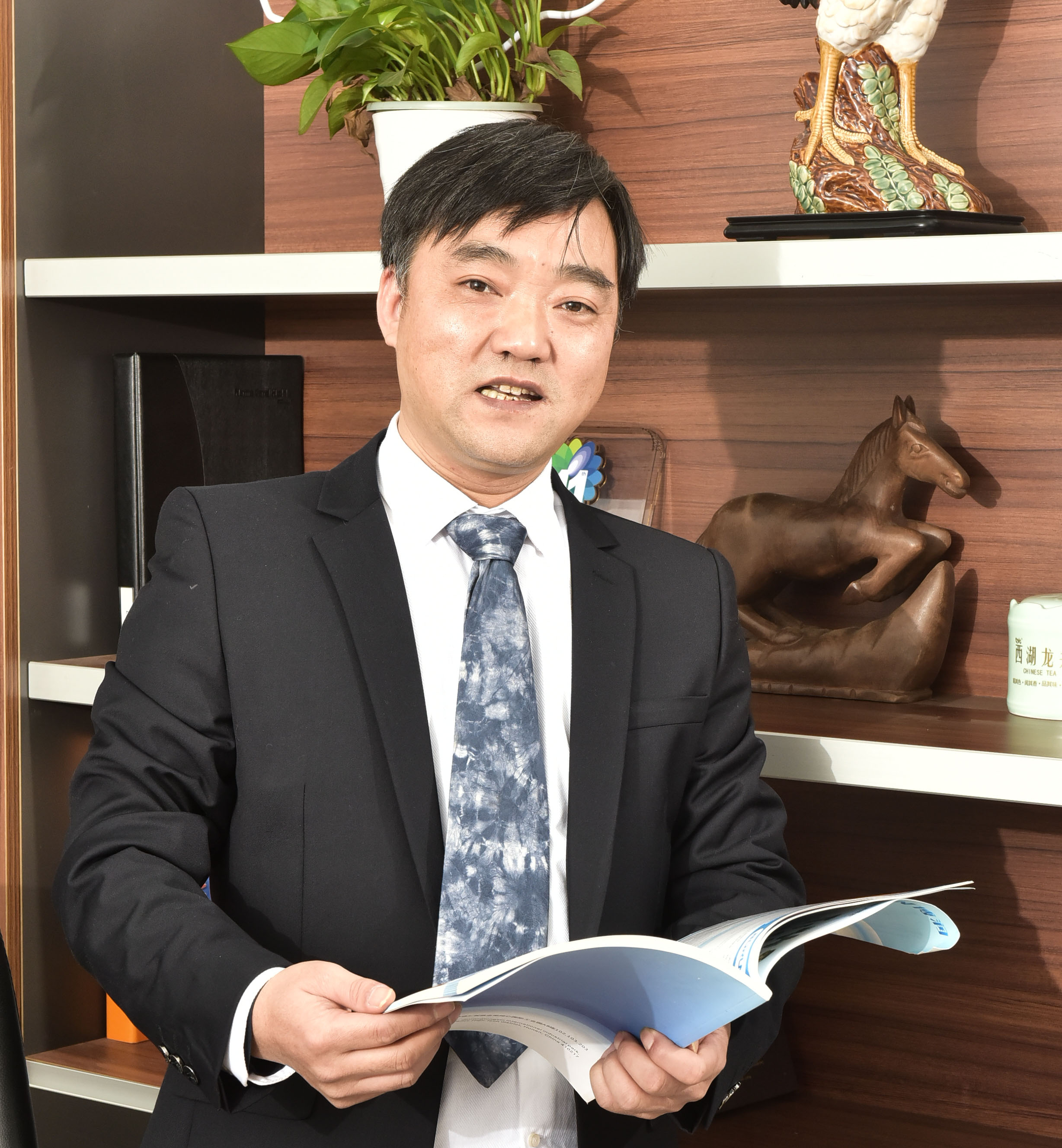
Mr. Tony
Leave a messageMr. Tony
Leave a messageAs precision plastic, stamping mould processing manufacturers, often need to purchase the corresponding Mold Parts, among them, the quality of die parts directly determine its service life, therefore, a lot of plastic, stamping mold processing plant more and more pay attention to the durability of the mould parts.As you know, everything needs to be repaired and maintained in the process of use. Next, we will share the details of the maintenance of spare parts for injection molding and stamping die processing factory.
In the process of the use of the mould, it is necessary to continuously inspect and repair the mold. Of course, the preventive measures should also be carried out, and the regular maintenance of the Mold parts will play a crucial role in the service life of the molds.The annual maintenance procedure required for each injection molding position depends on the different mould cycle, how to repair the mold parts and so on.
1. Check whether there is an early warning of rust or moisture in the loose hole.
If you find rust or humidity near the vent hole, it means that the internal condensation, or the water pipe, may break.Moisture can cause a fatal short-circuit to the heater.If the machine is not running all year round and needs to be shut down at night or on weekends, the chances of this condensation occur.
2. Check whether there is any sign of wear between the guide column and the guide suite.
Find out whether there are scratches or scratches, etc. The wear of this mold parts is due to a lack of lubrication.If the trace is just present, you can extend its life by adding lubricant to the guide column and the guide sleeve.If the wear is serious, we should replace the new parts.Otherwise, the cavity and core may not fit well, resulting in a thin wall of parts.Will increase.
3. Post a logo at a prominent place to remind the operator not to "clean" the hot tip of the gate.
If the operator happens to see a small piece of stainless steel at the Nozzle of the mold, it may be a point.Cleaning up what seems to be a hindrance often ruins the hot tip.Not to destroy the hot mouth, please before taking action, confirm the mouth type of hot runner system, and ensure that all operators are trained, can identify themselves are exposed to different types of tongue.
4. The resistance value of the interactive check heater.
You should have measured its resistance when you first started using a heater, and the end of the year is when you measure it again and compare it.If the resistance value is a fluctuation of plus or minus 10%, consider replacing the heater to ensure that it does not break down at critical moments in the production process.If the initial resistance has never been measured, measure once and use the value as reference data for future inspection of the heater.
5. Slide stop
Machines are used unlimitedly and must be maintained in this process.
6. Cleaning the thimble is recommended to wash thoroughly with mold cleaning agent every 6 to 12 months.
After cleaning, apply a layer of lubricant to the thimble to prevent chafing or breakage.
NITONI, As a China Precision Mold parts, Core Pin, Ejector Pin, Mold punch, Mold parts, Mold Components, Non-standard Precision Parts, Plastic mold parts , press die mold parts, manufactur and supplier,At present, The mould accessories products are mainly divided into Non-standard mold parts, Plastic mould parts, Press die mold parts, Die Springs, welcome to understand the customization.